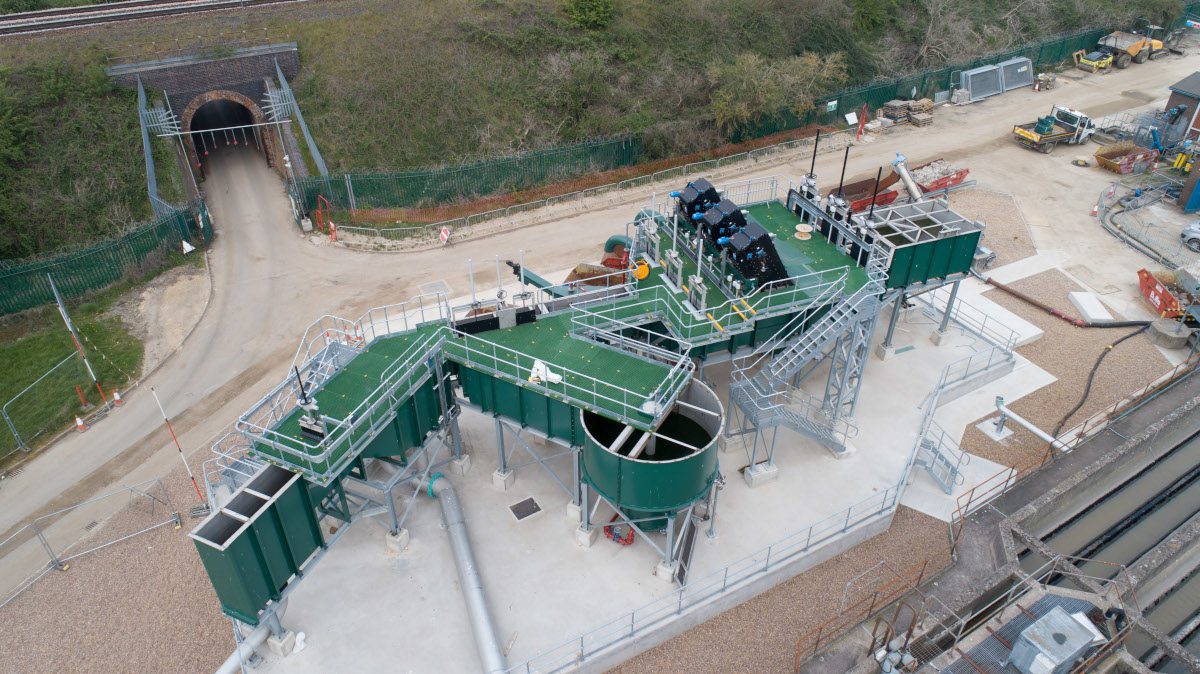
Screens revitalise inlet works
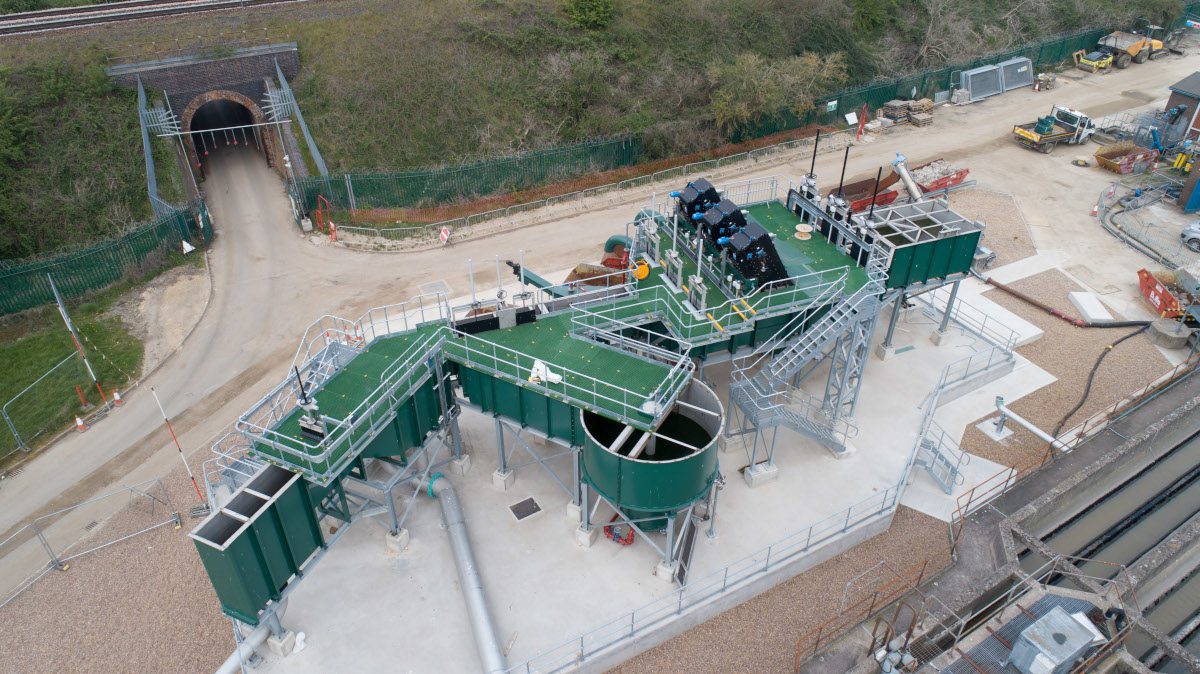
A prefabricated packaged treatment plant (constructed offsite) from SPIRAC has enabled a water visitor in the north of England to make much-needed improvements to its inlet works, and in doing so, alimony its stat footprint to a minimum.
For the Wastewater Treatment Plant that serves a population of 25,000, SPIRAC designed and built three of its proven FINEGUARD screens at its manufacturing plant so that there was minimal civils and no touchable pouring on site.
SPIRAC’s new treatment system sits on a reinforced precast touchable pad, supported by a galvanised steel support structure, elevated 5m whilom ground level. This allows flows to gravitate hands to the downstream process units.
Prior to the installation, the inlet could no longer cope with the volumes it was receiving. Rags were constantly bypassing the old screens and getting into the secondary treatment area.
Part of a £12.3M upgrade, the new treatment process has once resulted in key improvements to the quality of water stuff released into the local river. Surpassing the new investment, ammonia venting was at 13mg/l, but this has now been reduced to just 0.1mg/l.
SPIRAC’s three FINEGUARD screens are capable of passing a maximum spritz of 566 l/s of sewage at a diamond water depth of 1m downstream. Each screen consists of a wreath of perforated screen panels that are secured to momentum villenage on either side of the panels. On reaching the venting section of the screen, a self-adjusting skim mechanism (with water spray jets) cleans the screen panels of debris. This ensures that the oncoming spritz unchangingly meets unsullied panels for maximum performance. Furthermore, the screen panels are secured so that replacement of any individual units can be achieved with a minimum of effort and downtime.
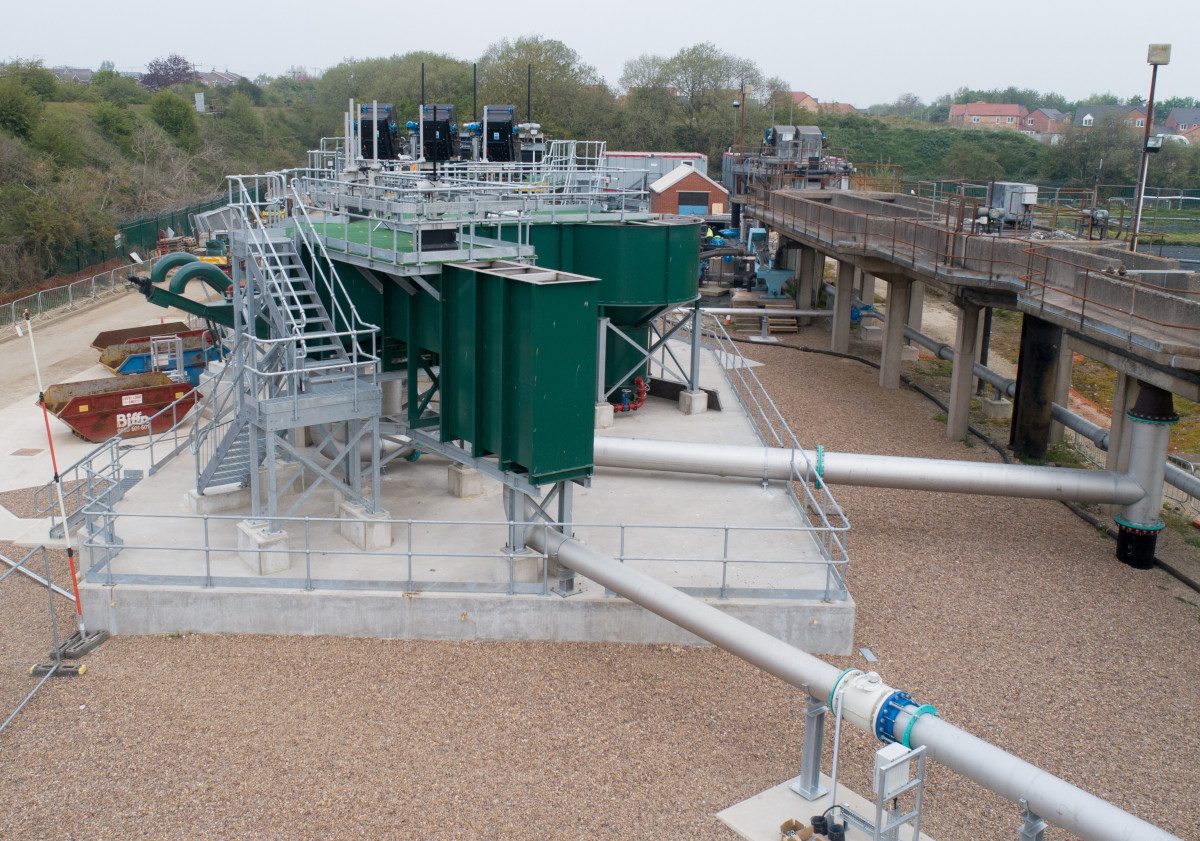
Screenings are transferred from the screens via a launder trough system. SPIROWASH units then wash out the organic material, reducing the volume and weight of the screenings by compaction surpassing delivering them to a skip via a printing tube.
A grit vortex unit moreover removes suspended grit from the sewage flow. This consists of a pre-fabricated grit vortex chamber capable of handling up to a maximum 628 l/sec of screened raw sewage flow. The grit is extracted by ways of a grit pump, and is fed to a SPIRAC SANDSEP grit separator unit capable of handling up to 20 l/sec of grit slurry. The SANDSEP unit dewaters and discharges grit into a skip.
Speaking for SPIRAC, Shyam Mallen said: “We are seeing far increasingly focus and demand from water companies and Tier One contractors to provide a well-constructed package, with minimal site time and use of civils materials, expressly concrete.”
He added: “With the comprehensive range of screens and grit removal solutions that we diamond and manufacture, we moreover have the topics to create significant savings for our customers. Offsite build, testing and wiring is a big goody for wastewater projects.”
More detail is misogynist on the firm’s website.